Масааки Имаи - Гемба кайдзен. Путь к снижению затрат и повышению качества
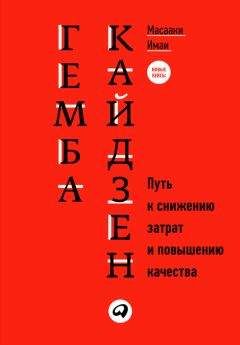
Помощь проекту
Гемба кайдзен. Путь к снижению затрат и повышению качества читать книгу онлайн
Начало пути
Оливер подводит черту под своими комментариями такими словами:
«Вышеописанные события иллюстрируют лишь несколько механизмов, способствующих вовлеченности и участию. Однако я полагаю, что фундаментальная задача состоит в том, чтобы продолжать преодолевать барьеры и представлять новые идеи, чтобы поддержать этот импульс. Компания Leyland – только в начале этого пути».
Усиливая логистику в компании Matarazzo
Аргентинская фирма Matarazzo of Molinos Rio de la Plata Company, входящая в группу компаний Bunge & Born group, – производитель свежих и сухих блюд из разных видов макаронных изделий. Готовую продукцию она поставляет в распределительный центр группы, расположенный в пяти километрах от завода.
На этом примере показано, как менеджмент в сфере логистики был усовершенствован за счет того, что для решения проблем в компании осуществлялся сбор данных, проводились наблюдения за производственными операциями в гемба, а также использовался подход, основанный на здравом смысле.
До начала реализации проекта кайдзен поставки осуществлялись ежедневно между шестью утра и шестью вечера; полное время, затраченное на каждую поставку (включая погрузку на заводе, перевозку, разгрузку в распределительном центре и возвращение на предприятие), составляло в среднем около трех часов. Шесть или семь грузовиков в день совершали всего от 10 до 14 перевозок. Кроме того, персонал, занимающийся поставкой, обычно должен был работать по субботам, поскольку не успевал выполнить все ежедневные задания, выдаваемые с понедельника по пятницу.
Поскольку производственные операции, связанные с погрузкой и разгрузкой, вынуждали водителя соприкасаться с продукцией, закрывая и раскрывая поддоны, товар часто повреждался. Другая нерешенная проблема заключалась в том, что грузовики надо было взвешивать четыре раза: дважды на заводе и дважды в распределительном центре (с продукцией и без нее). Для устранения неэффективности таких логистических операций и их оптимизации была организована группа кайдзен.
Спустя шесть месяцев после начала реализации проекта кайдзен руководство компании обнаружило, что требуются лишь два грузовика и четыре-шесть трейлеров. Продолжительность ежедневной работы сократилась на 7 часов и составила 11 часов. Время на выполнение производственной операции в расчете на один грузовик было уменьшено на 22 минуты (что означало усовершенствование на 88 %), а стоимость погрузки сокращена на 35 %.
Компания достигла этих результатов путем выполнения следующих кайдзен-действий:
• Согласно новым процедурам, к грузовику на заводе присоединяли загруженный трейлер. Водитель, доставив продукцию в распределительный центр, оставлял его для разгрузки, а тем временем к его грузовику присоединяли пустой трейлер, который затем возвращался на завод для загрузки. Потом водитель с новым загруженным трейлером вновь уезжал в распределительный центр.
• Распределительный центр сконструировал две разгрузочные платформы для их использования исключительно компанией Matarazzo.
• Трейлеры оснастили крышами специальной конструкции и перемещающимися шторами, чтобы устранить у водителей потребность вступать в соприкосновение с продукцией.
• Установили демонстрационный стенд, чтобы показывать вес каждого грузовика и трейлера. На нем были представлены все возможные комбинации, чтобы взвешивать грузы лишь один раз, а не дважды на каждом объекте.
Время, сэкономленное в результате внедрения этих усовершенствований, позволило увеличить ежедневное число рейсов, совершаемых водителем, с одного до пяти раз. И служащим теперь не приходилось работать по субботам.
Следующий шаг: кайдзен с точки зрения поставщика
Вскоре после того как новые процедуры были введены на местах, служащие отдела логистики и производственного участка сформировали группу, в которую вошли представители каждого из этих подразделений. В качестве основных были выбраны два направления деятельности: контроль качества продукции и производство. Из-за неоправданно длительных подготовительных мероприятий на заводе объем загружаемой и разгружаемой продукции был постоянно завышен, и обслуживание требовало в среднем около трех с половиной часов. Команда намеревалась предпринять кайдзен-действия, чтобы сократить продолжительность процесса обслуживания до менее двух часов. Для достижения этой цели группа сосредоточила свою работу на реализации следующих моментов:
• Разработка графика получения продукции, чтобы избавиться от нерешенных проблем и эффективно распределить работу вспомогательного персонала.
• Уведомление поставщиков о том, как улучшить планирование поставок.
• Определение приоритетов для поставщиков путем отнесения их к критическим или некритическим категориям на основе выполнения ими установленных требований к сфере деятельности.
• Установка плановых показателей по времени завершения разгрузки, а также быстрое обслуживание поставщиков, которые достигли этих показателей.
• Контроль времени, израсходованного на выполнение каждой задачи и каждого поставщика, как на самом заводе, так и вне его территории.
Спустя шесть месяцев после начала реализации кайдзен-проекта и после того, как было проведено 18 заседаний группы, время обслуживания поставщика сократилось в среднем до 70 минут. Поощренная этим достижением, команда установила новую цель: сократить время обслуживания до менее чем одного часа.
Расширяя сотрудничество, несколько подразделений компании представили отчет о времени, израсходованном в каждом конкретном случае (прибытие поставщика, время ожидания вне завода, время наблюдения за разгрузкой и время отбытия с завода). Поставщики приветствовали эту информацию, потому что она позволила им осуществить тщательный контроль над их собственным транспортом, в особенности зафрахтованным по договору. Полученные данные также поощряли поставщиков соблюдать согласованный график поставки.
Два месяца спустя время обслуживания поставщика сократилось до 45 минут. Как только вторая цель была достигнута, группа занялась стандартизацией задач и сбором данных, чтобы стабилизировать и поддерживать достигнутые целевые параметры, а также управлять ими. Наконец, в качестве альтернативы неавтоматизированному сбору сведений, который повлек за собой перепроверку по разным источникам, группа создала программу ведения базы данных, которая позволила получать мгновенный доступ к информации о выполненных действиях, о классификации по вводу информации и типу поставщика, времени обслуживания, результатах в сравнении с запрограммированными событиями и т. д. База данных позволила группе оформлять различные виды отчетов, резюме, краткие доклады и графики в зависимости от своих потребностей.