Владислав Подопригора - Бизнес-обновление 2.0
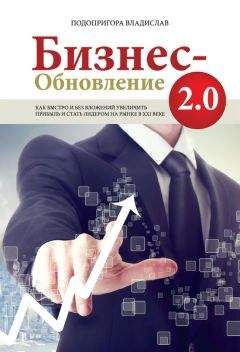
Помощь проекту
Бизнес-обновление 2.0 читать книгу онлайн
Для начала давайте договоримся о едином понимании понятия «управление производством». Это деятельность, которая включает в себя все действия, связанные с движением заказа от запуска сырья в производство до этапа готовности продукта к отправке заказчику. И в этой главе мы сконцентрируемся на том, как обеспечить в вашем производстве оптимальный баланс между сырьем и производственными ресурсами, требующимися для преобразования сырья в продукт, готовый к реализации.
9.1. Основные проблемы, мешающие производственной компании стать успешной
Перед тем как перейти к рекомендациям и призывам к действию, давайте комплексно рассмотрим, с какими проблемами чаще всего встречаются производственные компании.
Приоритеты на производстве постоянно меняются в зависимости от «важности» и «срочности» выполнения каких-либо заказов. Слишком часто отдел продаж требует от производства срочную поставку. Особенно большие проблемы возникают с планированием, из-за того, что заказ от клиентов и партнеров поступает позже, чем нужно было по технологической карте, и из-за постоянных корректировок размеров заказов.
Слишком много «проталкивания» заказов вручную руководством. Один мой клиент сказал, что раньше, ища еще одну лазейку, чтобы продвинуть заказ там, где мощности и люди были загружены под завязку, чувствовал себя в таких ситуациях как разведчик на войне.
Очень часто ресурсов нет в наличии, когда они требуются. Сырье/компоненты имеются не всегда, когда они нужны. Значительные объемы «незавершенки» между операциями технологического цикла приводят к замораживанию оборотных средств.
Необходимо постоянно модернизировать оборудование при ограниченных финансовых возможностях.
Слишком часто не хватает запасов каких-либо номенклатурных позиций. Причем чаще всего это самые востребованные позиции. И одновременно мы можем иметь в избытке другие виды сырья или полуфабрикатов. Большое количество устаревших номенклатурных позиций, которые не пользуются спросом. Склады затарены невостребованной продукцией, что приводит к замораживанию оборотных средств, с одновременной нехваткой нужной для рынка готовой продукции.
Всякий раз, когда в текущем процессе появляются отклонения, надо задать следующие вопросы: «Это случилось потому, что у нас не было стандарта? Это случилось потому, что мы не следовали стандарту? Это случилось потому, что стандарт не был адекватным?»
Масааки ИмаиВсе эти явления приводят к следующим негативным последствиям:
Регулярные конфликты между производственным подразделением и коммерческой службой, приводящие к нарушению психологического равновесия в коллективе.
Постоянные сбои в выполнении заказов, приводящие к тому, что клиенты воспринимают нас как нестабильную компанию, которой нельзя доверить крупный заказ. Все это становится причиной упущенных продаж и, соответственно, уменьшения прибыли.
У рабочих слишком много сверхурочной и повторной работы в пиковые периоды (аврал, конец месяца, сезон), а в остальные периоды рабочие недозагружены. В результате мы теряем деньги и из-за оплаты сверхурочных, и из-за вынужденного «простоя».
Для решения этих проблем я рекомендую начать управлять производственным процессом в соответствии с концепцией Теории ограничений систем, которая зарекомендовала себя в тысячах компаний во всем мире.
9.2. Главные секреты успеха в производстве
Мы будем применять аналогию, рассматривая производство как цепочку взаимосвязанных звеньев. Прочность цепи определяется прочностью самого слабого ее звена, которое и является ограничением. Бессмысленно укреплять иные звенья, кроме самого слабого, так как это не увеличит производительность системы.
Давайте вспомним о пяти универсальных шагах процесса непрерывного улучшения:
Шаг 1. НАЙТИ ограничение(я) системы.
Шаг 2. Решить, как МАКСИМАЛЬНО ИСПОЛЬЗОВАТЬ ограничение(я) системы.
Шаг 3. ПОДЧИНИТЬ этому решению работу всех остальных элементов.
Шаг 4. «РАЗВИТЬ» (расширить) ограничение(я) системы.
Шаг 5. Если в результате предыдущего шага ограничение(я) устранено(ы), вернуться к шагу 1. ПРЕДУПРЕЖДЕНИЕ: НЕ ДОПУСТИТЬ, ЧТОБЫ ИНЕРЦИЯ СТАЛА ОГРАНИЧЕНИЕМ СИСТЕМЫ.
Шаг 1 в производстве. Понять, какой станок, оборудование, цех, человек или любой другой элемент тормозит весь процесс производства.
Давайте для примера рассмотрим трехэтапное производство. За один час на первом этапе успевают обработать восемь изделий, на втором этапе – пять изделий, на третьем этапе – шесть изделий. Сразу понятно, что участок с наименьшей пропускной способностью – «Заточка» и что вся система производить больше чем пять изделий в час не сможет.
Чтобы найти слабое звено в вашем производстве, нужно совсем немного. В 95 % случаев это тот элемент, перед которым больше всего скапливается сырья и который больше всего загружен работой.
Шаг 2 в производстве. Придумать/решить, как максимально использовать ограничение.
Когда мы находим настоящее ограничение производства, то устранить его обычно непросто. Вместо этого нужно выжать из ограниченного ресурса максимум пользы, на которую он способен.
Чаще всего это решается быстро. Здесь хочу рассказать одну историю из жизни моего клиента. В компании, являющейся производителем мягкой мебели, выявили, что узкое звено – этап первичной сборки. Горы полуфабрикатов в цеху. Работа там была наполовину автоматизирована: было дорогое немецкое оборудование и бригада сборщиков.
Начали наблюдать за работой людей на участке. Мы увидели, что оборудование простаивает 15 минут утром, когда настраивают технику, 60 минут в обед, когда «законно» обедают, и около 15 минут, когда вечером убирают.
Сразу же установили новые правила: станок настраивает один человек, приходящий раньше всех, а убирает другой, который приходит позже, перерыв на обед сделали плавающим, чтобы не все вместе уходили, а по очереди.
Это сразу добавило 1,5 часа эффективности не только цеха, а всего производства, так как именно этот цех ограничивал результаты всей системы.
Шаг 3 в производстве. Управлять всей системой через ограничение.
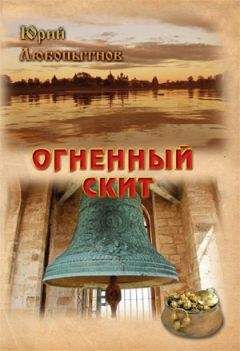
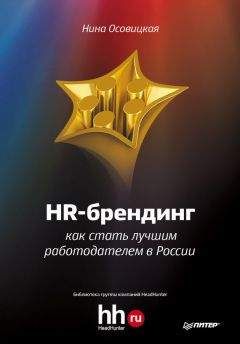
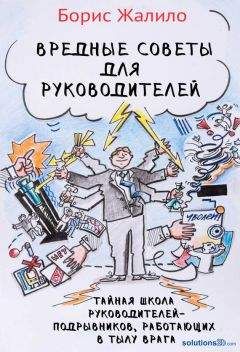
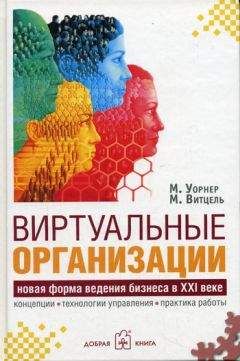
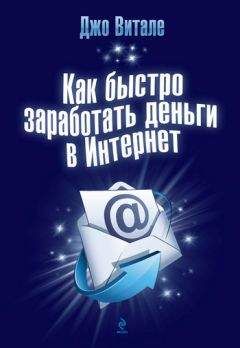